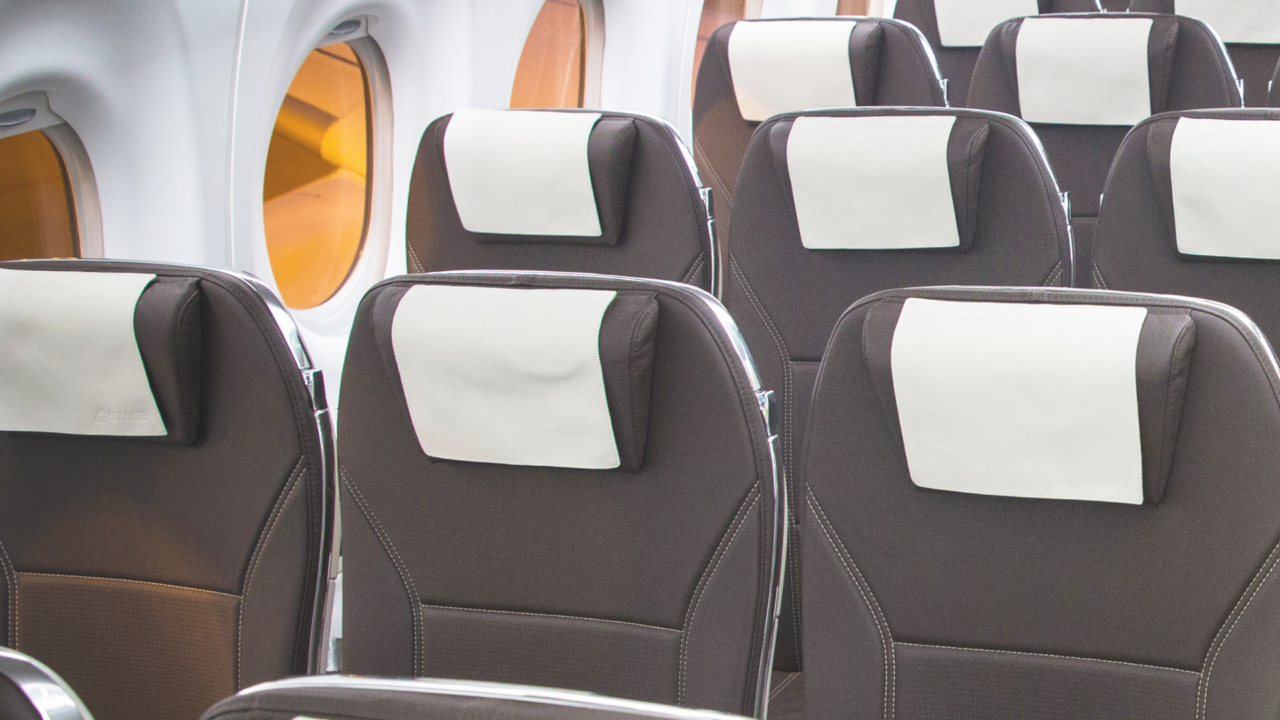
The aircraft industry is in constant evolution, with significant innovations in materials. As a result, it’s crucial to find the most suitable options for bonding these materials together. In aviation, several key factors are increasingly vital, including speed, lightweight construction, durability, design, and passenger comfort.
Technological innovations in aircraft interiors drive engineers and designers to seek the latest methods for improved performance continually. Moreover, this sector have stringent standards for aircraft interior applications.
How do Thermoplastic Adhesives Address Aircraft Challenges?
Thermoplastic adhesives in web, hybrid and film are suitable for wide-width bonding, offer numerous advantages for aviation applications and gives the solution to crucial aircraft specifications:
- Lightness: Bemis Protechnic Adhesive Web is lightweight (in g/sm) without compromising bonding strength, reducing the aircraft’s total weight. This optimization enhances fuel efficiency, thereby reducing environmental impact.
- Permeability: These adhesives allow air passage when bonded to materials with an open structure.
- Very Low VOC Content Adhesive: Thermoplastic adhesives with minimal VOC content contribute to reducing environmental impact.
- Performant bonding: Bemis Protechnic Adhesive Film due to it’s performances is suitable for applications in the aircraft that need full surface & strong bonding. (ex: honeycomb core)
Additionally, thermoplastic adhesives are resistant and durable while maintaining end product aesthetic and comfort.
What Materials Can Thermoplastic Adhesives Bond in Aircraft Interiors?
Thermoplastic adhesives are highly versatile and can bond a wide range of materials in aircraft interiors:
- Foams (e.g., PU Foam)
- Leather (Synthetic Leather and Natural Leather)
- Composites (ex: PP or aluminium honeycomb, carbon fiber, glass fiber)
Thermoplastic adhesive is a minor component within the FR-treated bonded structure. Protechnic’s thermoplastic adhesives successfully meet flame retardant standards, ensuring overall safety.
These adhesives play a crucial role in various aircraft applications such as seating, cabin dividers (accoustic insulation) or composite reinforcement.
Aircraft Interior Bonded Material Recyclability
Material recycling is a significant concern across industries, aiming to reduce environmental impact and contribute to a circular economy.
It is possible to recycle end-of-life aircraft interior bonded materials and waste materials through both mechanical and chemical processes.
The most important thing for recyclability is that your adhesive should be the same material as your substrates.
Are you an aerospace manufacturer? Do you need help for your bonding project? Contact our expert team at:
commercial@protechnic.bemisworldwide.com